在我国对原油依存度高企的时代,进口成本相对低廉的高硫原油成为我国石化行业的必然选择。但是,高硫意味着对石油化工设备以及环境保护提出了严峻的要求。近日,中国石油化工股份有限公司金陵分公司成功投产目前国内特大型的150万吨/年加氢裂化装置,用“循环经济”有效地解决了这个问题,为我国石化行业的可持续发展闯出了新路子。
化“硫害”为财富,循环经济效应初显
金陵分公司的生产现场,全封闭管线根根相接、环环相扣。高硫原油顺着管线进入炼油装置,令人生畏的“硫”却成为宝贵财富:含硫石油焦成了热电装置的燃料和即将改造成功的化肥水煤浆工程的原料,排出的含硫气体通过回收装置,生成了生产硫酸的原料硫磺,化肥水煤浆工程投产后生产出的氢气又作为炼油生产的原料,使用后的废渣则继续为热电装置提供燃料,而热电联合装置为整个生产链提供热能和电能……这条圆形的生产链中,生产原料被“吃尽榨干”,“硫”在循环利用中基本实现了“零排放”,减少了环境污染,一个“绿色石化”跃然而生。这正是中国石油化工股份有限公司金陵分公司(以下简称金陵石化公司)推进“循环经济”所带来的发展魅力。
有两方面的数据可以说明。一是在当前国际原油价格高位震荡的艰难市场面前,金陵石化抓住高硫、低硫原油价差较大的有利时机,规避原油高价位风险,大量采购含硫或高硫原油,降低原油采购成本,去年一年,采购和加工含硫、高硫原油426万吨,仅这一块就比使用等量低硫原油节约了8亿多元。去年公司利税18亿元,成本节约带来的效益功不可没。今年近半年来,原油加工量连创新高,保持了企业生产经营的良好态势;二是去年,金陵石化加工原油突破800万吨,同比增长了100多万吨,但与之相反的是,企业的废弃物的排放却大幅减少。这一反差的实现,源于企业内部建造的废弃物回收链,源于企业不断调整产品结构,建立的资源综合利用共生体系。
为什么?金陵石化充分发挥含硫装置的巨大作用,建立生产循环链,实现资源内部循环。随着加工高硫原油规模的扩大,金陵石化成为中石化集团公司加工高硫原油的基地,特别是1350万吨炼油改造全部完成以后,每年可生产大量的石油焦,其中大部分是高硫焦。为此,金陵石化先后进行了两次较大规模的含硫原油加工改造,第一次是在原油加工能力从500万吨增至800万吨时,第二次是在800万吨增至1350万吨时。两次投入加起来在20亿元左右,如果加上废弃物再利用等其他配套装置改造,共花了30亿元左右。今年,公司又投入巨资对化肥装置进行了原料路线改造,用水煤浆取代轻油做原料。巨大的技改投入也使金陵石化内部建立了资源内部循环的生产链条,使得炼油装置生产的石油焦既可为即将改造成功的化肥水煤浆工程提供原料,又可为热电联合装置提供燃料,同时化肥水煤浆工程投产后,不仅可降低生产成本,提供优质的尿素,生产出的氢气还可作为炼油生产的原料,而化肥水煤浆工程使用后的废渣又可继续为热电装置提供燃料,热电联合装置则可为整个金陵石化提供热能和电能。而硫磺回收装置则将排出的含硫气体全部予以回收,生成了生产硫酸的原料硫磺,实现变废为宝。生产循环链有效提升了金陵石化的规模效益,实现了清洁生产,也带来可观的成本节约,体现了循环经济:“低消耗、低污染、高产出"的内涵。
推行HSE管理体制,全方位推进循环经济
能够把“谈硫色变”的高硫变成财富,除了舍得投入,增强原油综合加工配套能力外,也得力于HSE体系建设。
石油化工是高耗能大户,如何摆脱传统的高投入、高消耗、高污染、低效益的发展模式?金陵石化始终坚持技术创新,走内涵发展之路,从2002年起建立了HSE一体化管理体系,全方位推进循环经济发展战略。
HSE管理是指健康、安全与环境一体化管理。它是一种先进的系统化、科学化、规范化、制度化的管理方法,也是当前石化行业进入国际市场竞争的通行证。在金陵石化HSE管理体系中规定企业法人是企业环境保护的第一负责人,对本企业的环保质量负责,是企业建设、生产、经营中环保行为的第一责任人,并承担相应的责任。每年公司和各厂、车间、专业公司签订“健康、安全、环境”责任状,环境保护是其中的一项重要内容。在这一体系运行下,金陵石化的“九五”、“十五”期间的各类技术改造工程,其中的环保概算投资总是占领了相当份额,工程在工艺选择、流程设计和设备选型时均充分考虑环境保护的因素,严格执行环境影响评价制度和环保“三同时"管理制度,确保增产不增污。
近几年来,公司还投入资金新建了高浓度污水与生活污水处理装置、含硫污水净化水回用系统、4万吨/年硫磺回收装置;扩容改造含油污水处理装置,增加7000立方米生化曝气池,将砂滤改造为后浮选;西套含硫污水汽提装置由35吨/时提高到100吨/时,1#硫磺回收装置处理能力由1万吨/年改至5万吨/年,使酸性气100%得到有效处理。大大提高了环境保护的硬件水平。HSE管理体系的推行使环境管理部分达到ISO14001环境管理体系标准,环境保护的管理水平逐步与国际接轨。
加强清洁生产,建立循环经济发展的流程体系
如果说HSE是制度保障,那么流程体系是执行制度的基础。清洁生产是发展循环经济的主要方式之一,它是指不断采取改进设计、使用清洁的能源和原料、采用先进的工艺技术与设备、改善管理、综合利用等新流程措施,从源头削减污染,提高资源利用效率,减少或者避免生产、服务和产品使用过程中污染物的产生和排放,以减轻或者消除对人类健康和环境的危害。
按照国家可持续发展战略方针,金陵石化于1997年开始在清洁生产工作的“人、财、物”方面大量投入,采用先进技术进行改造,生产清洁产品。以前油品的精制除去其中的杂质,通常采用酸碱精制,不但油品的品质不高,还产生大量酸碱渣,不仅处理需要投入大量的资金,还会造成对环境的污染。为此,金陵石化配套建设一套200万吨/年柴油加氢精制装置,即将再建一套250万吨/年柴油加氢精制装置,从而不但可以生产出质量远远高于酸碱精制的产品,还将其中硫、氮等变废为宝,生产高品质的硫磺和液氨。再加上芳烃联合装置的部分单元预加氢,保证生产出的汽油、柴油质量达到欧Ⅲ标准,部分产品可以满足欧Ⅳ标准,还可以为170万吨扬巴提供优质乙烯原料。
继含硫含氨污水汽提等装置成为中国石化集团公司清洁生产示范装置以后,又有加氢裂化、汽油加氢、40万吨/年的柴油加氢等多套装置获得国家、中石化集团公司和省级“清洁生产示范装置”称号,其中含硫污水汽提注碱脱固定铵工艺、二氧化碳回收综合利用技术、无压缩机浓氨水精馏法制液氨工艺等被评为清洁生产实用技术,在石化系统获得广泛应用。到2004年底金陵石化已实现清洁生产的装置达到了73%,通过持续清洁生产及采取有效节水措施,工业用水重复利用率达95.75%,实现了经济建设与环境保护的协调发展。
通过这些努力,金陵石化调整产品结构,构建资源综合利用的共生体系。特别是今年4月7日,目前国内特大型的150万吨/年加氢裂化装置在金陵石化开工投产一次成功,这一工程包括改扩建800万吨/年常减压装置、新建150万吨/年加氢裂化装置、新建160万吨/年延迟焦化装置和5万吨/年硫磺回收装置以及系统配套工程等项目,整个工程概算投资14.5亿元。这些装置的相继投产使金陵石化公司原油综合加工能力再上一台阶,达到1350万吨/年,同时调整产品结构,实现地区资源优化,产品结构也发生很大变化:
首先,促进了金陵石化成品油的升级换代,满足了新标准清洁燃料的市场需求。所生产的轻石脑油、航空煤油、柴油、汽油等产品达到了国家新标准规定的成品油质量要求,为中国石化今后开辟国内外新的成品油市场创造了条件。
同时,可以充分满足向扬巴工程提供优质原料。在确保成品油市场供应的基础上,大力调整产品结构,最大限度地多产化工原料,为扬巴提供优质石脑油,为南化公司提供硫磺,实现南京地区的资源优化。为了进一步满足市场需求,调整产品结构,做到宜“芳”则“芳”,宜“烯”则“烯”,公司即将全面启动60万吨/年PX装置,该装置的建成投产将为金陵石化精细化工的发展打下坚实的基础。
打造“绿色石化”,形成鱼与熊掌兼得的双赢局面
今年金陵石化将在去年的基础上再上一个台阶,预计全年将加工原油1100万吨,成为国内长江沿线首个千万吨级炼油生产基地。“十一五”期间,金陵石化还将改造一套800—1000万吨/年常减压装置,使原油加工规模达到1600—1800万吨/年,从而使金陵石化真正成为具有世界规模的高含硫原油加工基地,从而不仅进一步提升企业的竞争能力,也为市场提供充足的能源供应,为地方经济的发展作出突出贡献。
“循环经济”,已成为中国经济生活中的关键词之一。
正是通过发展“循环经济”,金陵石化在技术改造、资源综合利用、清洁生产实施方面取得了显著成效,据了解,近年来,金陵石化的废水排放综合达标率优于国家标准,工艺废气和燃料燃烧废气达标率100%,固体废弃物“三率"达100%。由于重视执行环境保护“三同时"和“以新带老"治理污染,实现了增产减污,环保治理效果不断提高,污染物排放总量和浓度逐年降低,先后荣获“南京市环境保护先进企业”、“江苏省环境保护先进企业”等荣誉。
金陵石化正逐步实现废物利用,变废为宝,把放错地方的资源不断再利用,着力打造一个“绿色石化”。而“绿色石化”给金陵石化带来的不仅是更为突出的社会效益,也为金陵石化的经济效益、可持续发展创造了良好的条件。
向规模要效益,向循环利用要效益,这将是金陵石化今后发展的重要思路。
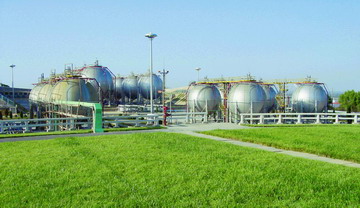
图为球罐区
|